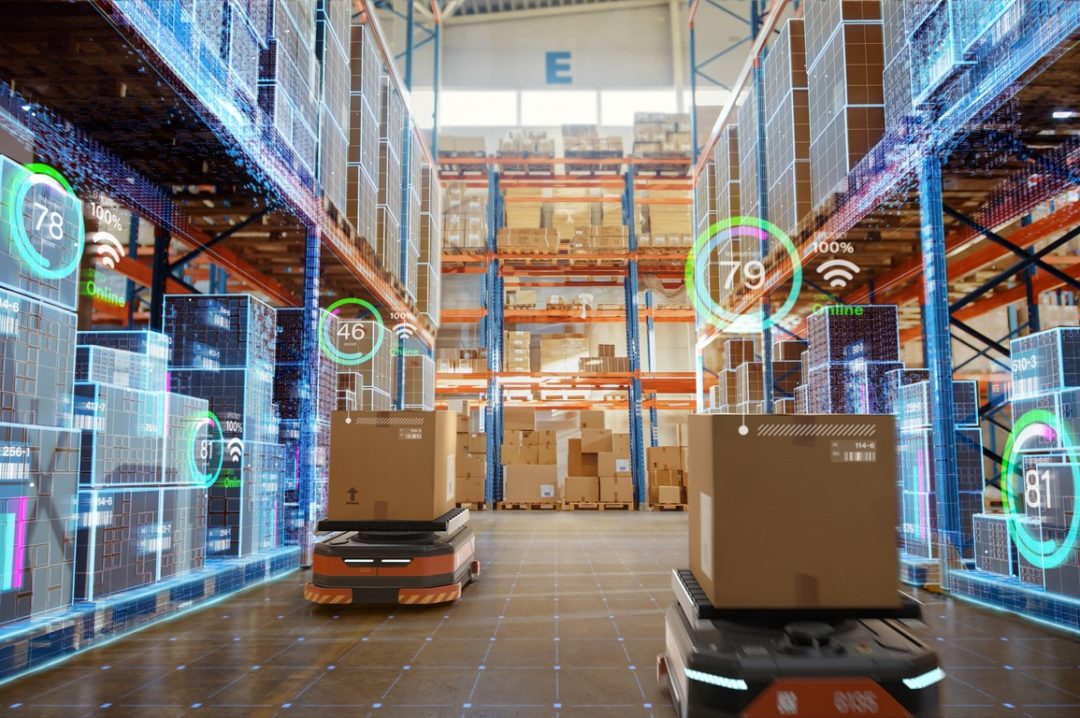
Photo: iStock.com/gorodenkoff
Warehouse Challenges? Automation Can Help
Warehousing operations have evolved dramatically in recent years, and traditional warehouses are challenged to deal efficiently with the demand variability, channel diversity and labor risks characteristic of today’s environment. Here are five challenges that warehouses face and how automation can help them succeed.
1. Seasonal Demand and Scalability
Supply chains are challenged with uncertain and unpredictable seasonal demands, but traditional warehouses struggle to scale operations in response to fluctuations. Fixed shelving and storage systems make it difficult to reconfigure warehouse layouts quickly to accommodate changing inventory needs. As a result, warehousing operations often acquire more space than they actually need.
Automated storage and retrieval systems (ASRS) maximize the utilization of warehousing space with a flexible bin system that responds to changes in demand in two ways. It allows space utilization to grow and contract dynamically and incrementally as volumes change, and it automatically reconfigures the location of bins to ensure that those containing faster-moving items move to the top, making those items easier to retrieve. These attributes promote flexibility and scalability, allow for denser storage of inventory, and enhance warehouse efficiency.
2. Product Slotting and Inventory Organization
Traditional warehouses struggle to adapt to changes in product mix and velocity. Warehouse managers analyze historical sales data and future open orders to identify fast-moving and slow-moving items to optimize slotting and to reconfigure product locations in response to changing demand.
Even if they use sophisticated software to analyze the data, it’s still difficult to determine whether relocating stored products will promote efficiency in any given situation. Without real-time data analysis, it’s impossible to optimize product location, and that leads to inefficiencies such as increased picking times and higher error rates.
Advanced technologies rely on real-time data to understand the relative velocities of stored products and allow operators to analyze data based on configurable date ranges appropriate to their business. These analyses can be performed dynamically to understand, for example, whether certain items move faster on weekends than on weekdays or if price reductions will accelerate velocity — and to relocate items accordingly.
Retailing businesses often operate on an 80/20 model — in which 20% of their products represent 80% (or more) of their sales. That’s why retail businesses, with their large number of products, but with a small subset of SKUs representing an overwhelming percentage of sales volumes, can particularly benefit from the inventory management innovations that automation can provide.
3. Order Picking and Fulfillment Efficiency
With manual picking methods, employees push wheeled carts from one open location to the next and are equipped with devices such as radio frequency scanners to record picks. Studies have shown that as much as 53% of employee time is spent traveling within the warehouse and searching for items to pick, yielding a slow and inefficient process.
Walking up and down warehouse aisles adds to worker fatigue, and, because manual picking processes rely on humans with varying skill levels, they yield unpredictable daily outputs. Manual workflows also cap the operation’s maximum throughput and don’t add value to warehousing processes.
Before the explosion in e-commerce, warehousing operations involved case picking, but those days are gone forever. In recent years, split case picking, break case picking, piece picking, and each picking — in other words, less than full-case picking — represent an increased proportion of warehouse activities. Picking accuracy and labor efficiency for individual item picking becomes even more important in such an environment.
Advanced systems, such as goods-to-person warehousing operations, bring products to pickers, over a conveyor or by robot. Goods-to-person systems eliminate the 53% of employee dead time, increasing the order picking and fulfillment efficiency of the operation. Applying automation not only makes picking operations more efficient, but it also increases labor productivity and reduces labor costs.
4. Omnichannel Fulfillment
Fulfilling diverse orders across different channels under one roof has become the order of the day for today’s warehouse operators. Before the advent and recent growth of e-commerce, warehouses were in the business of moving cases and pallets to retail stores. Nowadays, they’re also picking individual items.
Retail and e-commerce orders differ in quantity, frequency and customer expectations. Business-to-business (B2B) orders are usually fulfilled within 48 hours. The business-to-consumer (B2C) model operates on much more aggressive timelines.
Manual processes can’t optimize both channels simultaneously. That means that manual warehouses end up processing each channel in separate waves, which duplicates work and compromises efficiency. Workers go to the same warehouse areas to pick the same products multiple times for different fulfillment flows.
Automation allows warehouse operators to blend their B2B and B2C models, which reduces inefficiencies and allows them to process more freight. The system can instruct pickers to grab cases as well as individual units of a specific product to fulfill both retail and e-commerce orders, before sorting the picks to their respective staging areas for shipping.
5. Workforce Recruitment and Retention
Manual warehouses are finding it increasingly difficult to attract skilled and engaged workers. Warehousing jobs can be mundane, which drives down job satisfaction and leads to high turnover rates and retention challenges. Research suggests that it costs warehousing operators between $3,500 and $10,000 per employee turnover for recruitment and retraining.
Younger employees are often attracted to positions that offer modern and technologically advanced work environments. Tech-savvy candidates are reluctant to work in environments that use obsolete technology and employ inefficient processes.
Automation, far from eliminating jobs, makes work more enjoyable and rewarding for humans. Robots eliminate the walking time around a large warehouse, cutting down on employee fatigue and providing a safer environment. Automation also introduces the element of gamification to work environments — where the technology provides automatic and instant feedback to workers on their performance — a feature that many younger employees enjoy and appreciate.
In a tight labor market, human workers are not always available when crunch times come, but warehouses can scale up and scale down their fleet of robots as needed. Deploying automation reduces labor supply risk while enhancing the productivity and job satisfaction of a new breed of warehouse workers — those who want to work with the latest technologies.
AutoStore — Providing a Flexible, Scalable, and Modular ASRS for Today’s Warehouses
Many warehouses today still run manual systems in which employees direct workflows and spend much of their time walking up and down aisles to pick and slot products.
AutoStore’s automated storage and retrieval system (ASRS) turns that model on its head with “a system-driven, goods-to-person approach,” says Zach Isbell, an AutoStore business development manager.
“Inventory is stored in bins which fit into an aluminum grid structure, like a Rubik's Cube,” says David Jeziorski, an AutoStore business development manager. “Robots traverse the top of the grid to pick and retrieve inventory totes to bring to pickers. Over time our solution will slot the fastest moving SKUs to the top so they'll be retrieved faster.”
Because the solution is modular, like an erector set, it provides the flexibility to grow with a company’s revenues. “You don't have to build out for seven or ten years,” says Isbell. “You can build a two or three-year model and expand to meet incremental gains.”
AutoStore’s customers number over 1,450 around the globe, in the spare parts, hardware, retail goods and pharmaceuticals sectors, who benefit by maximizing space utilization and streamlining picking operations. “What may typically take 10,000 square feet of real estate in a traditional warehouse,” says Jeziorski, “can be consolidated by up to four times, down to 2,500 square feet.”
“And it can grow in any direction,” adds Isbell, “vertically, horizontally, and above or below mezzanines.”
The solution can also reduce picking time by 50%.
“That,” says Jeziorski, “dramatically reduces the costs of fulfilling orders.”
Resource Guide: www.autostoresystem.com